Lost Foam Casting Common Pitfalls and their Solutions – Why some foundries are struggling with LFC? – A detailed behavioural analysis.
However, many foundries across India and beyond struggle to adopt LFC successfully. These challenges typically arise not from the technology itself, but from avoidable errors in implementation, mindset, and approach.
If you’re planning to upgrade your foundry with Lost Foam Casting or are facing setbacks, this article will walk you through the most common Lost Foam Casting mistakes and how to avoid them through strategic action and on-the-ground experience.
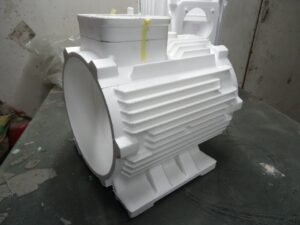

Mistake #1: Lack of Experienced Manpower and Consultants
Many foundries begin their LFC journey without adequately qualified professionals. Either they lack trained engineers or depend on consultants with insufficient hands-on knowledge of the (v-LFC) vacuum-assisted Lost Foam Casting process and its silent operational points and intricacies.
They may also consult the equipment manufacturers directly without considering – requirement analysis as per the casting product and future product plan, their plant layout, and operational strategy.
How to avoid it – Engage an LFC consultant who has proven holistic, instinct-based LFC experience and has a minimum of 15 years of exposure across Whiteside, Yellow-side, and Backside operations in an LFC shopfloor environment.
Theoretical knowledge or conventional sand casting experience alone cannot replicate the insights gained from LFC shopfloor problem-solving.
Mistake #2: Treating LFC Like Conventional Sand Casting
Too often, equipment is purchased or fabricated by copying conventional designs, without understanding the nuances of vacuum-assisted casting. Foundries misuse or misdesign equipment using low-grade steel, or overlook how foam pattern density, coatings, and vacuum impact casting quality.
How to avoid it – Before making investments, study the process holistically. Understand why each piece of equipment exists, how it behaves under vacuum, and how it complements other systems. Build with process-specific logic, not based on prior habits from traditional green sand or shell molding.
Mistake #3: Hiring based on bias instead of mindset
Foundries often rely on experienced conventional foundrymen who resist adapting to new technologies. Their expertise, while valuable in traditional processes, can become a barrier in vLFC due to “rigid thinking and a lack of dynamic evolution.”
How to avoid it – Hire a foundry manager who is open to learning and has the drive to adopt new techniques. For the rest of the team, prefer fresh ITIs, diploma holders, and engineers who can be trained from scratch without bias.
In LFC, a young mindset and adaptability often matter way more than prior experience in foundry operations. Some modern LFC foundries learn it the hard way!
Mistake #4: Neglecting the Power of On-Site Training
No amount of classroom learning or research papers can substitute for on-floor lost foam casting experience. In vLFC, even simple castings like pipe fittings and motor bodies behave differently.
Without first-hand exposure to these variables, foundries fail to produce saleable castings consistently.
How to avoid it – Implement structured shopfloor LFC training and handholding programs led by experts. Teach not just how, but why – why foam behaves differently, why coatings affect flow, and how vacuum stabilizes mold integrity.
Create a culture where the workforce is trained to dynamically evolve with every new casting.
Lost Foam Casting, as a technology, doesn’t behave like conventional sand casting processes. The Lost Foam Process has its instinct-based science and needs a professional on-site shopfloor handholding and training for your foundry team.
Mistake #5: Choosing the Wrong Mentor or Consultant
At the heart of every failed LFC transition is often the wrong choice of guidance. Foundry owners may unknowingly choose consultants who are either sales-focused or rely on outdated knowledge of the conventional casting process.
How to avoid it – Treat this decision with the gravity it deserves.
Choose a mentor or consultant who has a proven track record of executing LFC projects end-to-end on a turnkey basis, and who is willing to stay with your team on the floor, guiding them till castings are not just produced, but passed for sale! A mentor who serves even beyond the delivery of the project and maintains a long-term relationship.
Build Your LFC Success on Real Knowledge
Lost Foam Casting isn’t plug-and-play. It’s a living process that responds to foam density, vacuum pressure, coating density and thickness, and most-importantly, the team mindset. Foundries that succeed with LFC are the ones that combine process understanding with practical execution, day in and day out, with proper end-to-end consultation.
At GDM Technics, we don’t just offer consultation- we stay with your team, guide them on the shopfloor, and ensure your plant doesn’t just run, but thrives, practically teach your team to produce various successful and high-precision castings and get them approved!
Ready to avoid these mistakes and build a future-ready Lost Foam Foundry? Contact us today.
Mail: steel@gdmtechnics.com
Ph: +91-9200258915
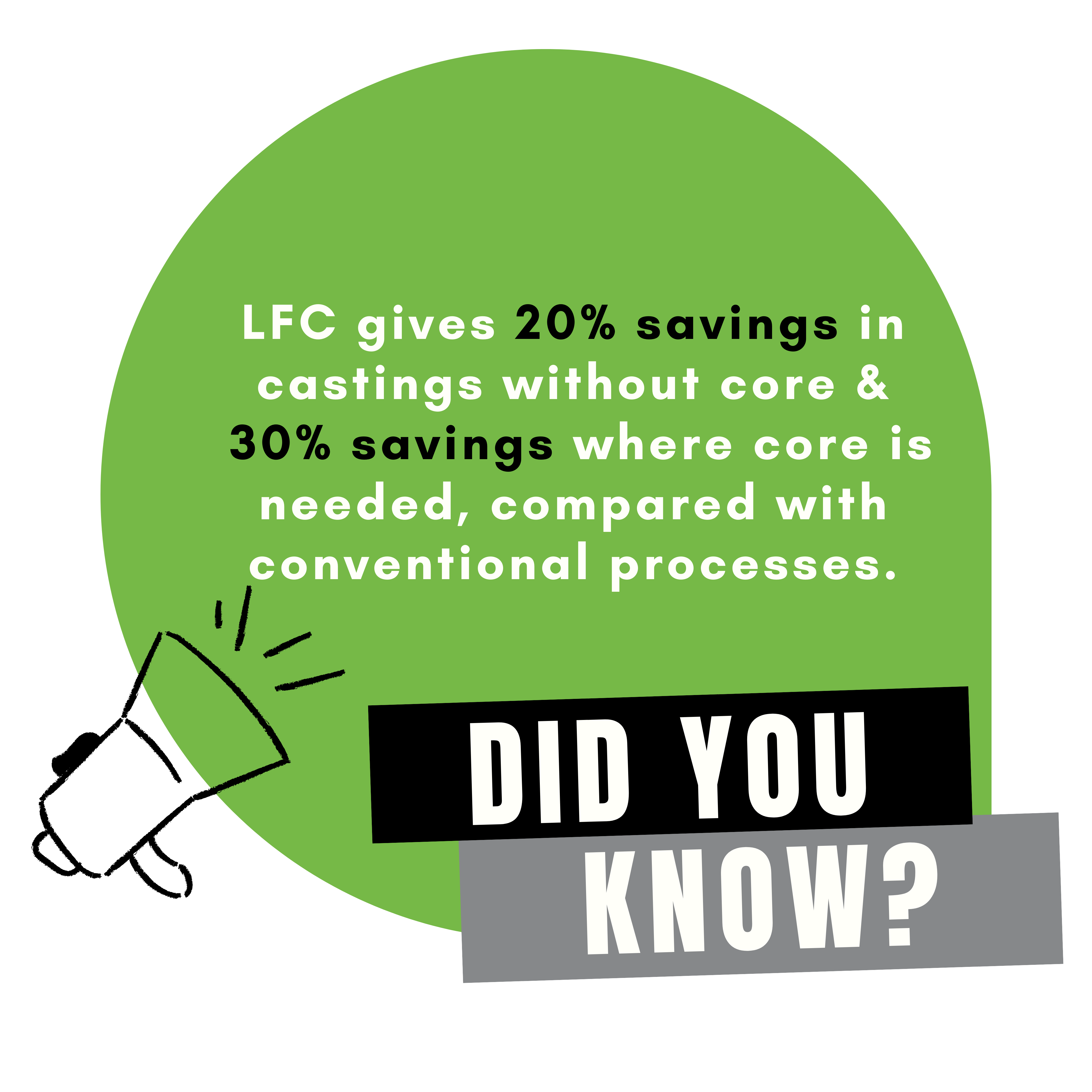
GDM Advantage
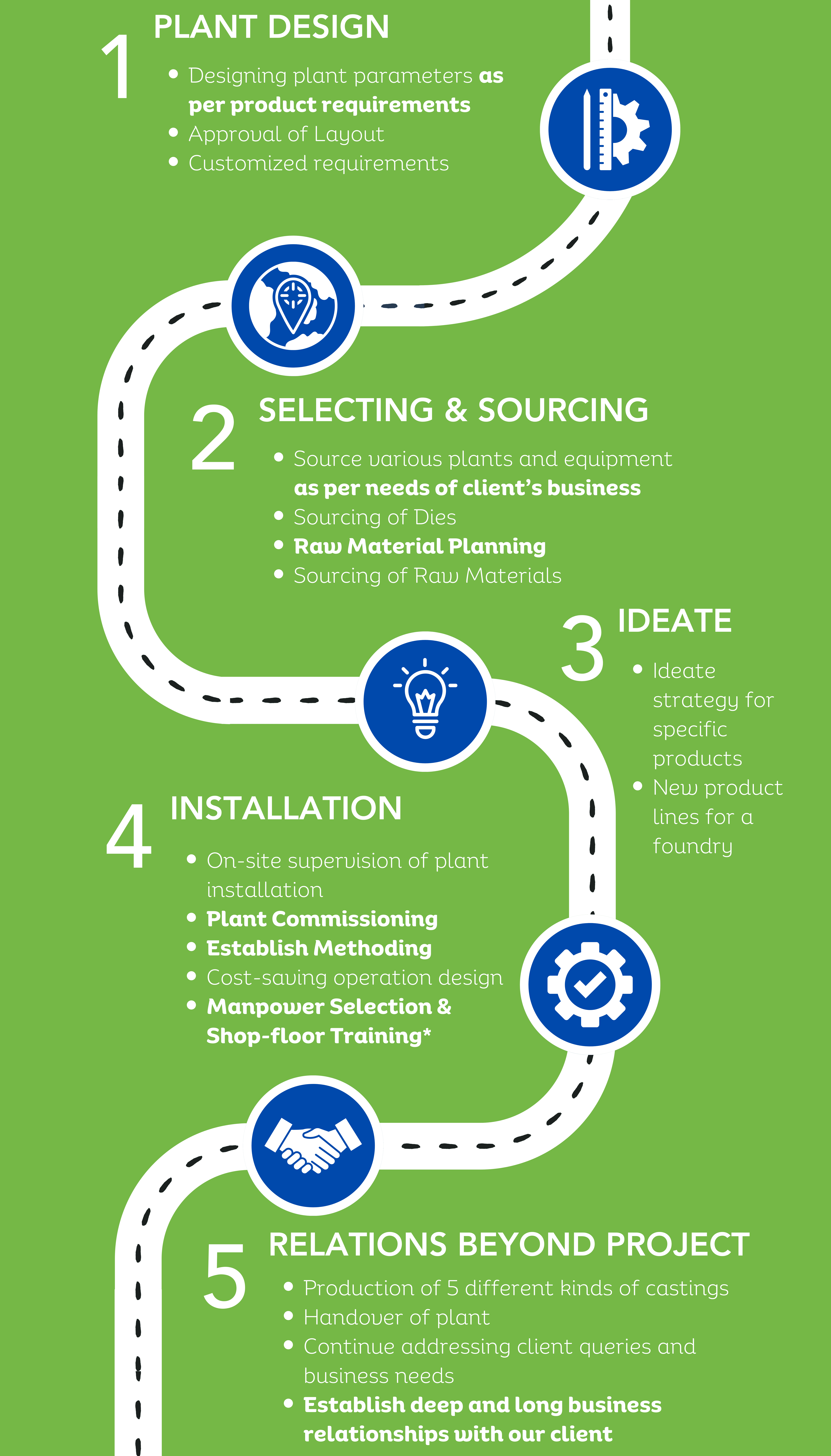
1 Comment