Introduction
In the world of metal casting, Lost Foam Casting (LFC) and Sand Casting are two widely used methods. This blog explores the key differences: Lost Foam Casting Vs Sand Casting, highlighting why LFC is the future of modern casting. While Sand Casting has been the traditional choice for decades, Lost Foam Casting is rapidly emerging as the superior alternative due to its precision, cost-effectiveness, and environmental benefits.
With advancements in foundry technology, manufacturers are now shifting to lost foam foundries to enhance efficiency and reduce operational costs.
Lost Foam Casting Vs Sand Casting
Sand Casting: The Traditional Approach
Sand Casting involves creating a mould cavity in the sand, into which molten metal is poured. The sand is then removed after solidification, leaving behind the cast part. This process, while simple and widely used, has limitations in precision, surface finish, and complexity.
Lost Foam Casting: The Modern Innovation
In Lost Foam Casting, a foam pattern is created, coated with a refractory material, and placed in unbonded sand. When molten metal is poured, the foam vaporizes, leaving behind an exact metal casting. This process eliminates the need for cores, parting lines, and additional machining—making it a more efficient and cost-effective method.
Lost Foam Casting Vs Sand Casting: Data Comparison
Feature | Lost Foam Casting (LFC) | Sand Casting |
---|---|---|
Design Complexity | Allows intricate, near-net-shape designs without cores | Limited by sand cores, making complex designs difficult |
Dimensional Accuracy | ±0.005 mm/mm, reducing machining effort | Lower precision, often requiring additional machining |
Surface Finish | Smooth (2.5–25 µm) with minimal finishing | Rougher surface requiring extensive post-processing |
Production Cost | 20-50% lower due to reduced material waste | Higher due to more material and machining requirements |
Material Efficiency | No risers or exothermic sleeves, reducing metal consumption | More metal is needed, increasing costs |
Eco-Friendliness | No chemical binders or sand wastage, making it a green process | Generates dust, requires chemical binders |
Energy Savings | 27% less energy is required compared to Sand Casting | Higher energy consumption |
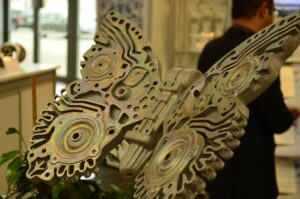
Why Lost Foam Casting is Superior to Sand Casting
1. Enhanced Design Freedom
Lost Foam Casting enables seamless integration of complex shapes, eliminating the need for sand cores. This means multi-part assemblies can be cast as a single unit, reducing weak points and enhancing durability.
2. Cost Savings and Material Efficiency
With no need for cores, binders, or extensive post-processing, Lost Foam Casting lowers production costs by up to 35% compared to Sand Casting. Additionally, 98% of the sand is reusable, making it a highly sustainable process.
3. Superior Surface Finish & Precision
Unlike Sand Casting, which requires extra machining, Lost Foam Castings offers a smooth finish (2.5–25 µm) with tight tolerances (±0.005 mm/mm). This means less grinding, polishing, and material wastage.
4. Environmental and Energy Benefits
Lost Foam Casting is a clean, dust-free process, eliminating harmful emissions and reducing energy consumption by 27%. In contrast, Sand Casting produces dust, requires chemical binders, and consumes more energy.
5. Faster Production and Reduced Waste
Lost Foam Foundries benefit from higher productivity (85-90%), while Sand Casting has a lower yield due to core-related defects. With LFC, rejections due to core shifting, inclusions, or surface defects are minimized.
Why Foundries are Switching to Lost Foam Casting
The advantages of Lost Foam Casting over Sand Casting are undeniable. With higher precision, reduced costs, and superior sustainability, lost foam foundries are becoming the industry standard for high-quality, complex metal castings.
If your foundry is looking to transition to Lost Foam Casting, GDM Technics provides turnkey LFC solutions, ensuring a seamless setup, optimized processes, and long-term profitability.
🔹 Want to set up a Lost Foam Foundry?
🔹 Looking to reduce costs and improve casting quality?
🔹 Need expert guidance on LFC technology?
📩 Get in touch today!
📧 Email: steel@gdmtechnics.com
🔗 Connect on LinkedIn: linkedin.com/company/gdmtechnics
🚀 Join the future of casting with Lost Foam Casting Technology!
2 Comments