Introduction to Lost Foam Foundry Technology
The Lost Foam Foundry process is an advanced metal casting technique designed for high precision, cost savings, and environmental sustainability. By eliminating the need for cores, binders, and parting lines, Lost Foam Casting (LFC) allows for complex metal castings with minimal machining.
With the growing demand in automotive, railways, defence, and industrial machinery, Lost Foam Foundries are revolutionizing India’s manufacturing sector by reducing material waste and optimizing energy use.
Why Lost Foam Foundry is the Future of Metal Casting
Lost Foam Casting stands out as one of the most energy-efficient and environmentally friendly casting technologies today. Key industry benefits include:
✅ Lower Energy Consumption → LFC reduces energy use by 27% compared to conventional casting.
✅ Cost Savings → Foundries experience 20-25% cost reductions, with savings exceeding 50% for complex castings.
✅ Eco-Friendly Process → Eliminates the need for harmful binders, producing zero crystalline silica pollution.
✅ Superior Casting Quality → Achieves dimensional accuracy of ±0.005 mm/mm with thin-wall castings as low as 3 mm.
✅ Optimized Material Use → Reduces metal consumption by 5-15% by eliminating unnecessary risers and exothermic sleeves
***(Reference: https://www.osti.gov/servlets/purl/1024103 , Page 106, Paragraphs 2 & 3)
How Lost Foam Foundry Works
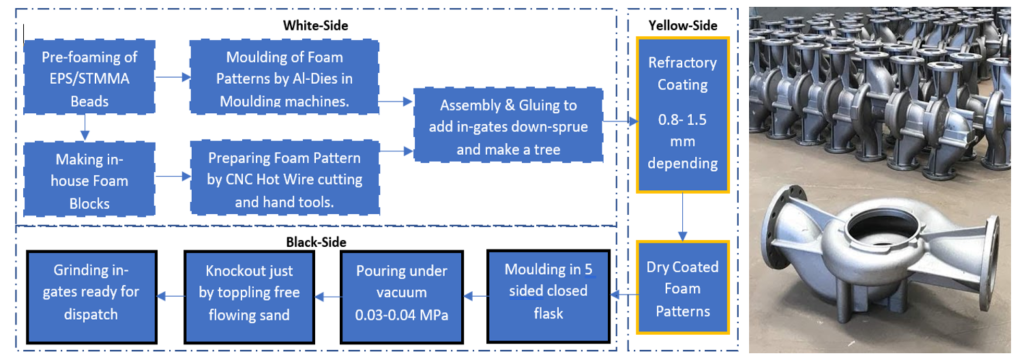
Energy and Environmental Benefits of Lost Foam Foundry
🔹 98% Sand Reusability → Unlike traditional casting, no chemical binders are required, making sand fully recyclable.
🔹 Zero Toxic Emissions → Foam vaporization is controlled, and gases are neutralized via catalytic converters before release.
🔹 20-25% Energy Savings → Reduced metal melting, machining, and fettling lower overall energy consumption.
🔹 Lower Workplace Hazards → Eliminates the risk of silicosis caused by fine silica dust, ensuring a safer work environment.
Lost Foam Foundry - Material Advantages: Ceramic Sand vs Silica Sand
🔹 Silica Sand Issues → Causes thermal expansion cracks, leading to defects in castings.
🔹 Ceramic Sand Benefits → Withstands 1850°C, offering a better surface finish and 10X longer life than silica sand
🔹 Lower Sand Consumption → Ceramic sand reduces usage by over 99%, making foundries more sustainable and cost-effective.
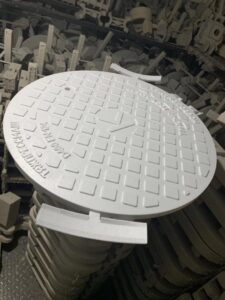
Meet GDM Technics at IFEX 2025 in Kolkata – The Leading Consultant for Lost Foam Foundry Project
Join GDM Technics at IFEX 2025 in Kolkata, India’s premier foundry exhibition, where we will showcase cutting-edge Lost Foam Foundry Solutions tailored to modern manufacturing needs.
Meet our GD Mishra of GDM Technics at IFEX 2025 in Kolkata – The Pioneer Consultant for Lost Foam Foundry Project and V-Process who introduced both these Moulding Processes in India.
With decades of expertise, Mr GD Mishra at GDM Technics will be available for one-on-one discussions on turnkey Lost Foam Casting (LFC) projects – foundry setup, process optimization, and cost-saving innovations.
🔹 Customized Foundry Setup & Design – Optimized plant layouts for maximum efficiency.
🔹 Advanced Equipment Sourcing & Installation – Integrating high-precision LFC machinery for seamless production.
🔹 On-Site Training & Process Optimization – Equipping your workforce for high-yield operations.
🔹 Sustainable & Cost-Effective Solutions – Helping foundries achieve up to 50% cost savings and 27% energy reduction.
📍 Visit Us at IFEX 2025, Kolkata
📅 Dates: 9th, 10th, 11th February 2025
📌 Venue: IFEX-2025, Biswa Bangla Mela Prangan | Kolkata
For appointment scheduling, contact us today:
📩 Email: steel@gdmtechnics.com Ph:+91-9200258915
🔗 LinkedIn: linkedin.com/in/modernfoundry