Lost Foam Casting in India: Revolutionizing foundry operations with precision and efficiency
Lost Foam Casting in India is fast becoming a transformative technology in the foundry sector, with industries across the country adopting it for its precision, cost-efficiency, and environmental benefits. This advanced method offers a way to produce complex, high-quality metal castings, making it an ideal choice for foundries seeking precision, reduced waste, and lower costs.
As pioneers in Lost Foam Casting (LFC), GDM Technics has led the development and adoption of this technology across major industrial hubs like Bhilai, Raipur, Rajkot, Ludhiana, Kolhapur, Belgaum, and Coimbatore, and now also in Cairo, Egypt. Our expertise lies in providing complete, end-to-end turnkey solutions that meet the unique needs of each foundry and its future products. Here’s an in-depth look at how Lost Foam Casting is shaping India’s foundry industry and the advantages it offers.
What is Lost Foam Casting?
Lost Foam Casting (LFC) is a process where a foam pattern, usually made from polystyrene, is created in the shape of the final casting. This foam pattern is coated with refractory material and then surrounded by unbonded sand. When molten metal is poured into the mould, the foam vaporizes, leaving behind a perfect, high-precision casting in its place. LFC is particularly suitable for complex designs that are difficult to achieve with traditional casting methods, which makes it an excellent choice for a range of metals, including iron, steel, aluminium, and magnesium.
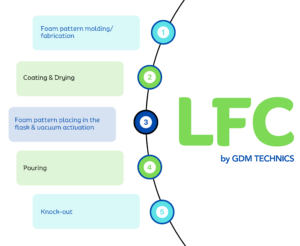
Lost Foam Casting Process
Advantages of Lost Foam Casting in India
The demand for Lost Foam Casting in India is growing as foundries recognize the technology’s unmatched benefits.
Here are some key advantages:
- Cost-Effectiveness: LFC offers substantial cost savings, with reductions of over 30% in manufacturing expenses for castings without cores.
- Enhanced Precision: By eliminating parting lines and draft angles, LFC achieves dimensional accuracy and a high surface finish, reducing post-casting machining requirements.
- Material Versatility: Lost Foam Casting supports various metals, making it adaptable for a wide range of industrial applications.
- Environmental Benefits: Reusable sand and reduced material waste make LFC a sustainable, eco-friendly option, aligning with India’s increasing emphasis on green technology.
Lost Foam Casting Process by GDM Technics
We offer comprehensive project consulting, from designing efficient foam patterns to setting up fully operational Lost Foam Casting foundries.
Our proven methodology ensures smooth and effective project execution:
- Pattern Design and Molding: Foam patterns are die-molded or fabricated to replicate the final casting’s exact shape. We use a meticulous approach to pattern-making, ensuring precision and efficiency in the final product.
- Refractory Coating and Drying: The foam pattern is coated with a refractory material to withstand the high temperatures of molten metal. Once dried, this coating enhances the durability and precision of the casting.
- Moulding and Sand Compaction: The coated foam pattern is placed in a flask filled with unbonded sand, which vibrates to ensure an even compaction around the pattern. Vacuum assistance enhances mould integrity, leading to cleaner castings.
- Molten Metal Pouring and Foam Vaporization: As molten metal is poured into the mould, the foam vaporizes, making way for the metal to form the precise shape of the casting.
- Knock-Out Phase and Finishing: After cooling, the casting is removed, and the sand is recycled, making the process sustainable and cost-effective.
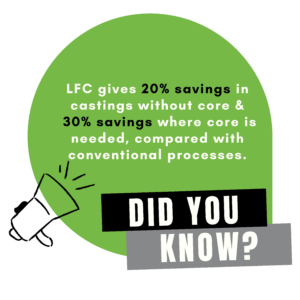
Lost Foam Casting Efficiency
Lost Foam Casting in India: Applications across industries
With Lost Foam Casting in India, industries from automotive to aerospace and steel plants benefit from the technique’s adaptability and quality. Its applications are extensive:
- Automotive Components: Lost Foam Casting is used in manufacturing engine blocks, cylinder heads, and other complex parts that require intricate designs.
- Industrial Machinery: Components like pump casings, valve bodies, and motor housings are precisely cast using LFC, enhancing their durability and reducing production costs.
- Railways and Infrastructure: LFC is ideal for producing heavy-duty parts for railways and large infrastructure projects.
Future of Lost Foam Casting in India
As India’s industrial sector continues to expand, the demand for Lost Foam Casting will only grow. This technology provides foundries with a way to modernize their processes, enhance profitability, and meet the demands of a competitive global market. With our commitment to innovation and sustainable practices, GDM Technics is proud to lead this change, bringing efficient and eco-friendly casting solutions to foundries across India.
Partner with GDM Technics for Lost Foam Casting Success
With GDM Technics as your partner, your foundry can experience the full benefits of this advanced technology. Our expertise, turnkey solutions, and dedication to client success make us the ideal choice for establishing high-performance Lost Foam Casting facilities.
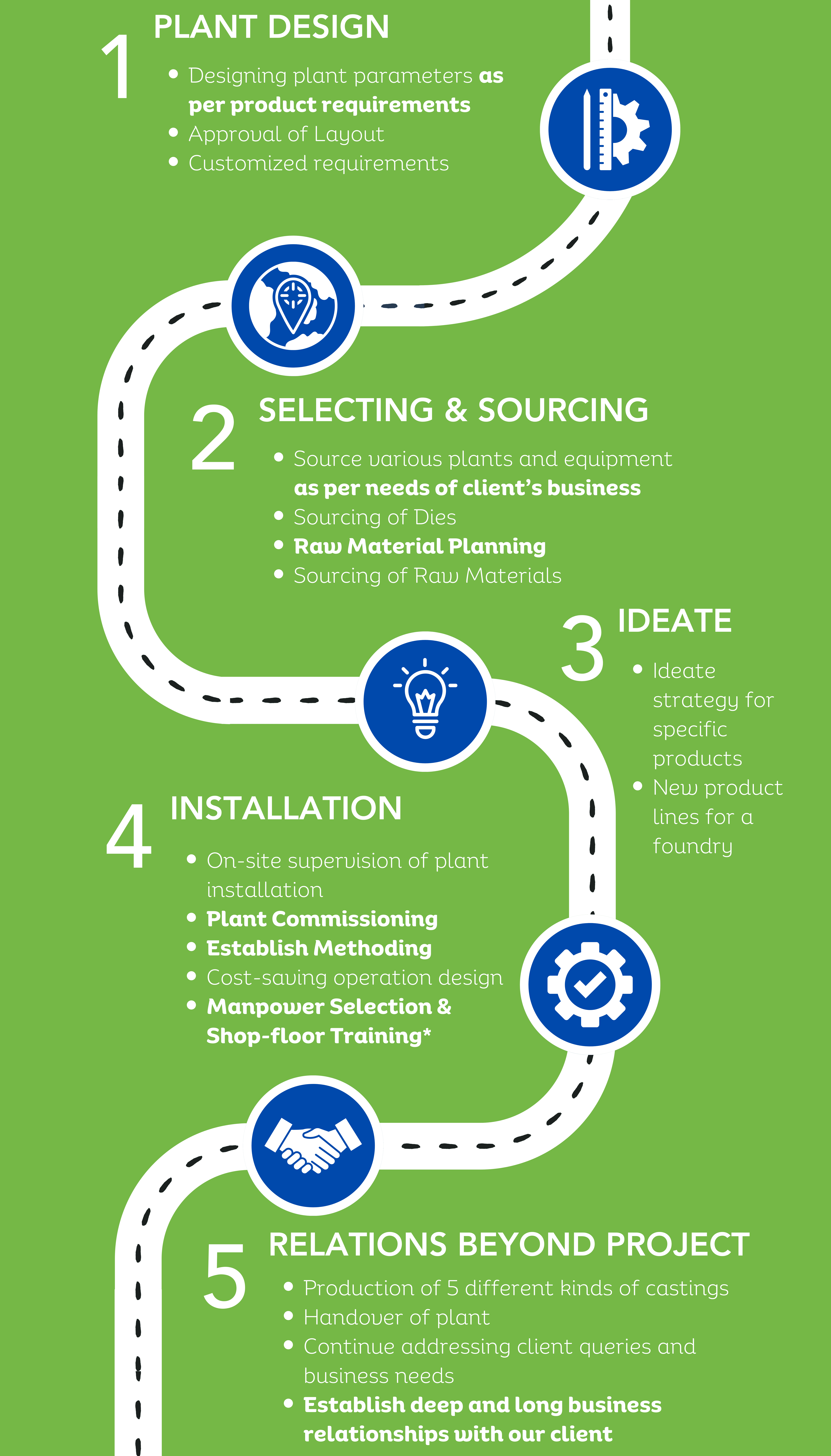
GDM Technics Services
Contact us today to explore how we can help your business thrive with Lost Foam Casting technology.
1 Comment